Is your cobot configured for optimal performance?
Is your cobot configured for optimal performance?
Cobots – or collaborative robots – are robots that are designed to work alongside human employees in various industries, from manufacturing and healthcare to warehousing and education. Often faster, lighter, safer, and more efficient than their industrial robot counterparts, businesses have increased their adoption of cobots over the years. In fact, we are currently seeing a much higher overall growth rate of cobots in recent years, compared to traditional industrial robots.
As cobots are on the rise with more and more companies deploying them – another question arises for many business owners: is your cobot configured for optimal performance? In this article, we will look at the importance of maximizing your cobot’s productivity, as well as several ways you can consider to further increase the efficiency of your automated operations.
The importance of optimizing your cobot’s performance
All businesses want to improve their operational capacity and efficiency without compromising production or service quality. An increase in cobot performance can mean higher output, better output, or both. This can lead to improved bottom lines, and achieving better margins is certainly one of the core motivators of all businesses.
Additionally, purchasing a cobot may not be as expensive as it used to be as they have become more accessible in recent years. However, cobots are still an investment with an upfront cost that is not insignificant – especially when purchased in multiples. Maximizing their performance also helps businesses pay off the cost of the cobot faster, increasing their ROI within the same timeframe.
How to optimize your cobot’s performance
When looking to optimize your cobot’s performance, you should understand the actions taken will depend on what the cobot needs to do and how the goals it needs to meet. Therefore, the first step is to look for areas upon which you would like to improve.
- Identify goals and improvement areas
It is important to first review the cobot’s work environment and tasks to see what specifically needs to or can be improved upon.
For example, in manufacturing, typically, cobots are deployed to automate tasks like picking, placing, and palletizing. They may be stationed along an assembly line with a specific task, or they may be deployed on a workbench to assist workers.
To optimize a cobot’s performance, then, may mean looking into increasing quality of products assembled by increasing precision. It may also mean increasing the speed of work by optimizing the use of space and incorporating sensors.
On the other hand, in healthcare, optimizing a cobot’s performance may be more related to operational safety. Building managers may seek to increase a cobot’s spatial awareness when placed in a room with patients, carers, and healthcare professionals.
- Leverage cobot software
Once you have identified some goals and ways to improve a cobot’s performance, the next step is to find ways to reach them. A lot of the time, this can be achieved by leveraging add-ons in software, which can be configured in cobots.
Using the previous examples – in manufacturing, increasing a cobot’s production speed or accuracy may mean using additional visual detection software to increase precision. For example, Universal Robots often provide vision software add-ons that allow their cobots to gain added sensing functions.
In a healthcare scenario, optimizing a cobot’s performance may mean incorporating visual or spatial software and setting safety parameters into a cobot’s configuration. One may teach a cobot to stop when they sense a moving object in proximity distance to avoid collision. Voice commands may also be configured to trigger actions.
- Optimize end-of-arm tooling
Of course, software is only half the battle for many businesses who rely on cobots to perform routine tasks such as picking and placing, palletizing, shelving, and more. This is where hardware optimization comes in. Cobot end effectors can be upgraded to increase precision and efficiency, depending on the application.
Several factors that should not be overlooked are gripping force, adaptability, and ease of integration with the cobot. Using the right end effector can be a game-changer, and it can even allow the cobot to be used in more ways than one, from cutting, grinding, sanding, to painting and welding. Coupled with the use of sensors in robotic systems, cobots can gain the ability to perceive their environment and respond most optimally.
Keep cobot performance optimal with routine checkups
Once you have improved your cobot’s performance, you may be tempted to leave it alone. However, the key to sustained improved performance is to conduct routine checkups on your cobots and their performance. Just as you would perform maintenance checks on other hardware you employ, such as healthcare equipment, forklifts, and cranes, cobots are not exempt from upkeep, despite being lower maintenance than traditional robots.
Final words
Whether you are operating a warehouse or running a busy clinic, cobots can be helpful companions that not only take the burden of routine tasks off your employees but also improve your bottom line. The key lies in identifying where they can be optimized and finding the right approach to maximize performance. To sustain improved performance, business owners or floor managers should also routinely evaluate cobot operations to ensure that everything is on track.
By
Monika
More Services
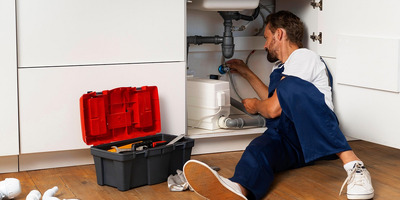
Sewer Pipe Comparison: Which Material Suits Your Home Best?
Different sewer pipe types impact home drainage and repair costs. PVC, cast iron, and polypropylene each offer unique benefits. Choosing the right material depends on your specific needs. This article explains these options and helps you pick the best sewer pipe for your home.
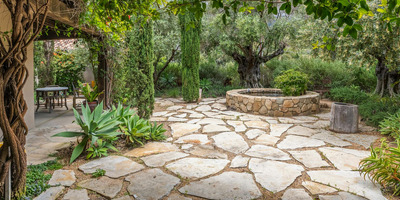
Flagstone Landscaping: Benefits, Installation Tips, and Maintenance Guide
In this article, we explore flagstone as a durable, natural material ideal for walkways, patios, and garden paths. Flagstone resists shifting, heavy impact, and harsh weather, offering long-lasting strength and aesthetic appeal for outdoor landscaping projects.
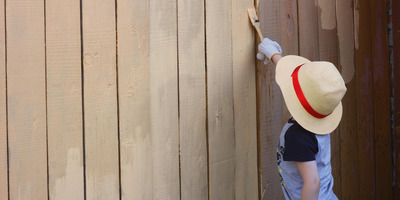
Fence Maintenance Tips: How to Keep Your Fence Looking New
Fences face wear from wind, rain, sun, and snow. Regular care prevents costly damage and keeps fences looking good. In this article, we will focus on tips to protect your fence from weather damage, with advice for wood, metal, and vinyl fences included.
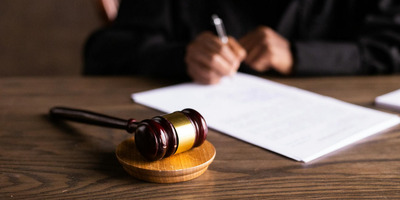
Understanding Bail in Canada: A Guide to the Process
Being arrested in Canada can be confusing, with the bail hearing being a crucial step. Bail determines if an individual stays in jail or returns to society while awaiting trial. Understanding bail laws often requires an experienced lawyer to build a case and ensure proper representation.
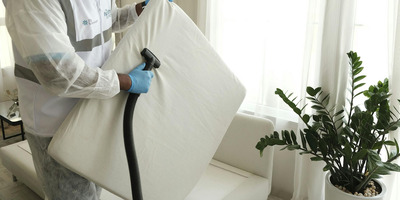
The Heat Solution as an Effective Bed Bug Treatment
Bed bugs disrupt sleep and cause anxiety. Heat treatment, a popular and effective pest control method in Canada, raises temperatures to eliminate bed bugs at all stages. Understanding its process, benefits, and limitations helps homeowners choose the best solution for their situation.
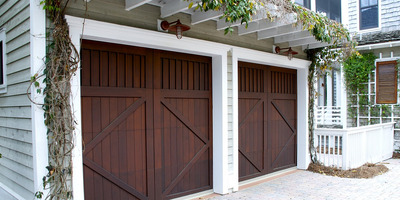
Revamping Your Entryway: Innovative Garage Door Design
Design experts from HGTV assert that a simple garage door renovation can significantly transform your home's exterior. This guide will navigate you through revitalizing your entryway with cutting-edge garage door designs from premier decor websites.
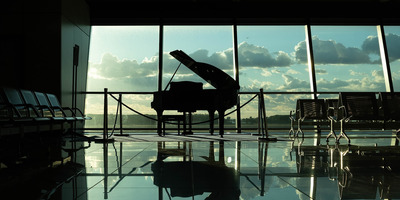
Should A Piano Be Tuned Before Moving?
The piano is one of the biggest, heaviest, and most sensitive musical instruments. Of course, the delivery of a piano or grand piano expects extremely cautious and thorough operation in all aspects, including setting up, using, storing, and, most importantly, transportation.
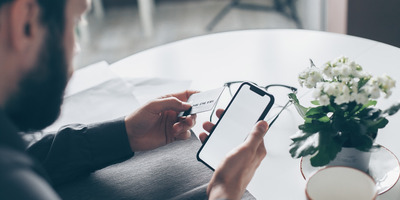
An Online Scam Can Happen To Anyone – Will You Be Prepared?
Once you get burned by milk, you'll blow on cold water. The same thing's true about getting scammed. If you fall for a phishing attack, a spam offer, a crypto scam, or something totally different, you'll treat every new email as a potential threat.